Bell Helmets DOME R&D Lab Tour
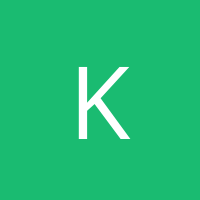
Where helmets are designed and smashed
Bell Powersports invited us to tour its American R&D and design facility this week so we could see with our own eyes the care and dedication that goes into the creation and testing of its head-protection efforts. It was enlightening to learn all that goes on behind the scenes at its Scotts Valley, California, location.
Bell was originally founded in 1923 as Bell Auto Parts, as it was based in Bell, California. It became one of the leading helmet manufacturers in the 1950s, and in 1963 F1 driver Jim Clark became Bell’s first world driving champion. As of 2016, Bell is under the Vista Outdoor umbrella and operates its Bell Powersports division to produce motorcycle helmets, along with its Giro and Blackburn bicycle helmet brands. The manufacturing of Bell’s helmets takes place in China.
Inside its Scotts Valley location are 140 employees using an office area for administrative and design activities, as well as a fabrication shop with three CNC mills, a 3-D printing room and, most interestingly, its testing facility where helmets undergo brutal impact testing. Dubbed as DOME (Design, Observation, Materials and Engineering), the lab includes drop testing and angled-impact testing that proves the worth of reducing rotational impacts via Bell’s MIPS (Multi-Directional Impact Protection System) and Flex movable helmet liners.
MIPS is one of the latest advances in head protection, as the shock-absorbing inner structure is designed to slightly rotate on impact – slip-plane-technology – to reduce rotational forces caused by angled impacts that can damage a brain. MIPS liners are said to achieve a 30% reduction in rotational forces, so you’ll be hearing a lot more about them being incorporated into new helmets in the near future.
MIPS is currently found in Bell’s Moto-9 motocross lid and its new Star MIPS and RS-2 helmets. Additionally, the high-end Race Star and Pro Star are equipped with Bell’s proprietary three-layer Flex liner that also damps rotational forces. Development time for new helmet ranges from just 12 months for simpler designs, but the Flex system required five years of evolution before it hit the market.
Scroll down to see pictures from inside DOME and watch a couple of videos of impact testing.
The video above shows a rig designed in-house by test lab engineer Patrick Burke at Bell. Here’s a traditional drop test at the Snell Foundation’s 7.75 meters/second velocity, the highest speed among motorcycle helmet impact tests. This particular test registered 192 g, well below the Snell limit of 275 g (in a size medium headform). Bell’s engineers say a 2-inch drop of a bare head would yield about same g force on a human skull!
This video shows Bell’s MIPS sled, one of just two in the world (the other is at the MIPS facility in Sweden), built at a purported cost of around $200,000. This test, operated by engineer Clint Hostetler, is what is called a “backwards” drop. Ouch!
We were fascinated by this tour with Bell and trust it was enlightening for you, too. For more on Bell, we invite you to check out its Powersports website.
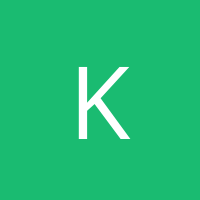
More by Kevin Duke
Comments
Join the conversation
Correction.... I just read it ..... I wouldn't buy a Chinese bike, why would I protect my head with a Chinese helmet? Just my opinion .... but if you are gonna exploit an American brand, at least make it in the USA.
I really like "behind the curtain" looks into the industry like this, which MO does better than anyone. It takes a lot more work than reprinting manufacturer specifications the way most sites do.
Mr. Duke, didn't Bell roll out a custom-fit program where they'd laser measure your head and build a one-off helmet just for you? Maybe I'm confusing them with another brand. I never heard anything about it since the MO article a year or so back.